Summary:
Belt Conveyor Roller Design: Key to Optimizing Material Handling Efficiency
Optimization principles for Belt Conveyor Roller Design
Future Development Trends of Belt Conveyor Roller Design
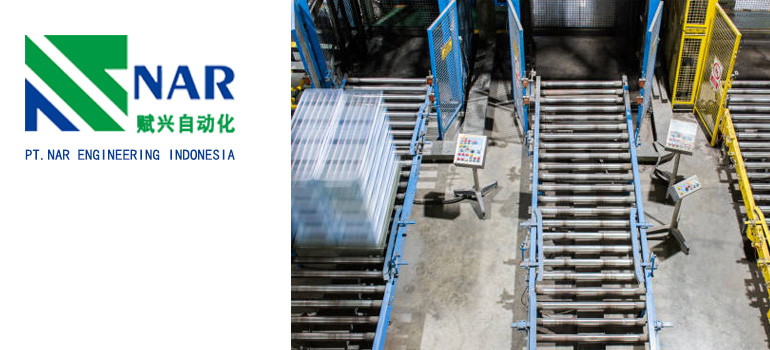
Belt Conveyor is one of the most commonly used material conveying devices in the industry. It can efficiently transport materials from one location to another, thereby improving production efficiency. In the entire conveyor system, the roller, as one of the key components, plays a crucial role in conveying efficiency and system stability. This article will delve into the design principles, optimization methods, and future development trends of the belt conveyor roller, aiming to provide valuable references for optimizing material conveying efficiency.
Optimization principles for Belt Conveyor Roller Design
Peralatan design of the belt conveyor roller has a significant impact on the efficiency and stability of the entire material conveying system. By selecting roller bearings correctly, designing the ratio of roller diameter to bandwidth reasonably, optimizing roller material and surface treatment, as well as layout and support structure, transportation efficiency can be improved, energy consumption can be reduced, and system life can be extended.
When designing conveyor belt rollers, the following points need to be given priority consideration.
- Load capacity and bearing selection: When designing the Belt Conveyor Roller, the primary consideration is its load-bearing capacity. It is necessary to ensure that the rollers can withstand the expected material load and maintain stable operation. When selecting roller bearings, it is necessary to consider their wear resistance, lifespan, and lubrication method to ensure the reliability and continuous operation of the system.
- Ratio of roller diameter to bandwidth: The ratio of roller diameter to bandwidth directly affects the stability of materials during transportation. If the diameter of the roller is too small, it will lead to uneven distribution of materials on the bandwidth, increase the wear of the bandwidth, and reduce the lifespan of the system. Therefore, it is necessary to choose the roller diameter reasonably based on the properties of the material and the conveying distance to optimize the conveying efficiency.
- Roller material and surface treatment: The selection of roller material and surface treatment directly affect its service life and material friction coefficient. For heavy load and high wear environments, wear-resistant and corrosion-resistant materials should be used, and the surface of the roller should be treated reasonably, such as hard chromium plating, coating, etc., to improve the wear resistance and material transfer efficiency of the roller.
- Roller layout and support structure: The layout and support structure of the rollers should be reasonably designed based on the characteristics of the material and the transportation route. Increasing the support point of the roller can reduce the deflection of the roller, thereby reducing energy consumption and reducing roller wear.
Future Development Trends of Belt Conveyor Roller Design
As a key component of the belt conveyor system, the optimization of its design and future development trends will directly affect the efficiency of material transportation and the sustainable operation of the system.
By continuously improving bearing technology, innovative material technology, application of intelligent technology, and environmentally friendly and energy-saving design, we can continuously improve the performance of the belt conveyor roller and achieve more efficient, stable, and environmentally friendly material transportation.
Improvement of bearing technology: With the development of technology, bearing technology will continue to improve, and more wear-resistant and durable bearings will be applied in the belt conveyor roller to improve the bearing capacity and service life of the roller.
Innovation in material technology: New high-performance materials will be applied to the manufacturing of rollers to improve their wear and corrosion resistance, thereby reducing system maintenance costs and downtime.
The application of intelligent technology: With the popularization of Internet of Things technology, belt conveyor roller will achieve intelligent management and monitoring. Sensors and data acquisition equipment will be integrated into the roller to monitor its operation status and wear degree in real time, so as to achieve Predictive maintenance and improve the reliability and stability of the system.
Environmental and energy-saving design: In the design of the belt conveyor roller, more consideration will be given to environmental and energy-saving factors. Adopting efficient roller design and bearing technology to reduce friction loss and energy consumption in the system, achieving green and environmentally friendly material transportation.
The optimization and improvement of conveyor belt bearings can improve the conveying efficiency and service life of the conveyor.
If you would like to know more about the conveyor content, please contact PT. Nar.
Maybe you are interested in the following: Key to improving production efficiency: Feed Belt Conveyor